Durable industrial laminated decals are an essential component of any business that requires labeling or identification of products, equipment, or machinery.
These decals are constructed using multiple layers of materials that are designed to withstand harsh environmental conditions and heavy usage. The lamination process ensures that the decals are resistant to fading, scratching, and peeling, making them ideal for use in industrial settings. They are available in a wide range of colors, sizes, and designs, and can be customized to meet the specific needs of a business.
What are Industrial Laminated Decals?
Industrial laminated decals are a type of label or sticker that is designed to withstand harsh environmental conditions and heavy usage. These decals are constructed using multiple layers of materials, including a base layer, adhesive layer, and a protective top layer made of a clear, durable laminate material.
Where to Use Industrial Laminated Decals?
- Product labeling: They are commonly used for product labeling in manufacturing and distribution settings. These decals can be customized with product names, logos, barcodes, and other important information to help with inventory management and tracking.
- Equipment identification: They are often used to identify equipment, machinery, and tools in industrial settings. These decals can include information such as serial numbers, model numbers, and maintenance schedules, making it easier to keep track of assets and ensure that they are properly maintained.
- Warning signs: They are frequently used as warning signs in industrial settings to alert workers to potential hazards. These decals can include text and graphics that warn of dangers such as high voltage, moving machinery, and hazardous chemicals.
- Safety labels: They are also commonly used as safety labels in industrial settings. These decals can include information such as safety instructions, emergency contact information, and first aid procedures.
- Asset tagging: They can be used for asset tagging, which involves labeling equipment and other assets with unique identifiers to help with inventory management and tracking.
- Branding and marketing: They can be customized with company logos, slogans, and other branding elements to help promote a company’s products and services.
- Instructional labels: They can be used as instructional labels to provide workers with information on how to use equipment or perform specific tasks.
- Control panels: They are often used on control panels to identify switches, buttons, and other controls.
- Machinery and tools: They can be used to label machinery and tools with important information such as maintenance schedules and safety instructions.
- Vehicles and transportation equipment: They can be used to label vehicles and transportation equipment with information such as vehicle numbers, maintenance schedules, and safety instructions.
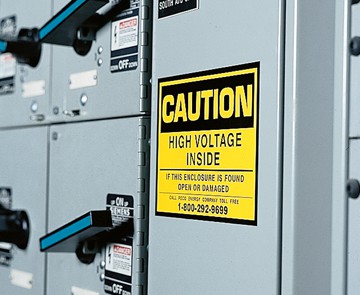
What are Industrial Laminated Decals Made Of?
The base layer is typically made of vinyl or polyester and is printed with the desired design or text using high-quality inks that are resistant to fading and scratching. The adhesive layer is designed to adhere to a variety of surfaces, including metal, plastic, and painted surfaces. The top layer, made of a clear laminate material, protects the decal from damage due to exposure to UV rays, moisture, and other environmental factors. Industrial laminated decals are available in a wide range of sizes, shapes, and colors, and can be customized to meet the specific needs of a business.
Industrial Laminated Decal Product Features
- Multiple layers of materials
- Resistant to fading, scratching, and peeling
- Durable laminate top layer
- Adhesive layer that adheres to various surfaces
- Available in a wide range of sizes, shapes, and colors
- Customizable to meet specific business needs
- Can withstand harsh environmental conditions and heavy usage
- UV resistant
- Moisture resistant
- Chemical resistant
- Abrasion resistant
- Easy to apply
- Cost-effective
- Enhances safety and organization in a workplace
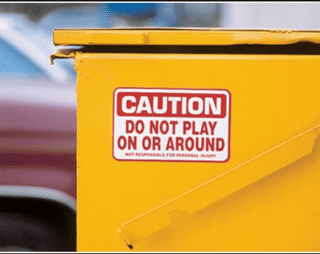
Are Industrial Laminated Decals Water and UV Proof?
They are designed to be resistant to water and UV rays. The top layer of the decal is made of a clear, durable laminate material that protects the decal from damage due to exposure to UV rays and moisture. This layer acts as a barrier, preventing the underlying layers from being damaged by these environmental factors. Also, the adhesive layer is designed to adhere to a variety of surfaces, including those that may be exposed to water or moisture. The use of high-quality inks that are resistant to fading and scratching also contributes to the durability of the decals.
Which is Better or Stronger, Vinyl or Laminated Decal?
Vinyl and laminated decals are both durable options for labeling and identifying products, equipment, and machinery in industrial settings. Vinyl decals are made of a single layer of vinyl material and are generally less expensive than laminated decals. They are easy to apply and can be used in a variety of applications. However, vinyl decals are not as resistant to environmental factors as laminated decals.
Laminated decals, on the other hand, are constructed using multiple layers of materials, including a base layer, adhesive layer, and a protective top layer made of a clear, durable laminate material. This makes them more resistant to fading, scratching, and peeling than vinyl decals. Laminated decals also provide better protection against UV rays, moisture, and other environmental factors.
What is the Difference Between Laminated and Non-Laminated Decal?
The primary difference between laminated and non-laminated decals is the presence of an additional protective layer adhered over the printed areas of the laminated decals. Laminated decals are constructed using multiple layers of materials, including a base layer, adhesive layer, and a protective top layer made of a clear, durable laminate material. This top layer provides an additional level of protection against environmental factors such as UV rays, moisture, and abrasion.
Non-laminated decals, on the other hand, are made of a single layer of material and do not have this additional protective layer. This makes them more susceptible to fading, scratching, and peeling over time. While non-laminated decals may be less expensive than laminated decals, they are generally not as durable and may need to be replaced more frequently. Laminated decals are a more reliable option for industrial use, as they provide better protection and are more resistant to wear and tear.
How Long Does Industrial Laminated Vinyl Decals Last?
The lifespan of industrial laminated vinyl decals can vary depending on a variety of factors, including the quality of the materials used, the environmental conditions in which they are used, and the level of wear and tear they are exposed to. However, in general, industrial laminated vinyl decals are designed to be durable and long-lasting. The top layer of the decal is made of a clear, durable laminate material that provides protection against environmental factors such as UV rays, moisture, and abrasion. This layer helps to prevent the underlying layers from being damaged or fading over time.
In addition, the use of high-quality inks that are resistant to fading and scratching contributes to the longevity of the decals. With proper care and maintenance, industrial laminated vinyl decals can last for several years, making them a cost-effective solution for labeling and identifying products, equipment, and machinery in industrial settings.
Conclusion
Durable industrial laminated decals are a reliable and cost-effective solution for labeling and identifying products, equipment, and machinery in industrial settings. While they may be more expensive than non-laminated decals or other labeling options, industrial laminated decals are generally considered to be stronger and more durable, making them a more reliable option for industrial use.
Popular Posts: